PVC Profile Co-Extrusion Line for Soft & Hard PVC
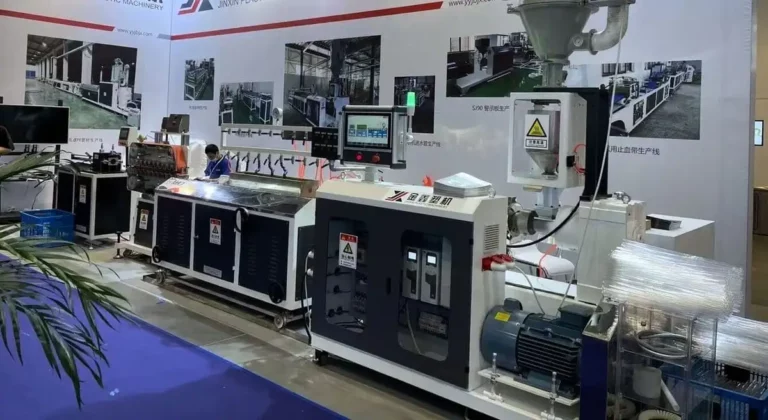
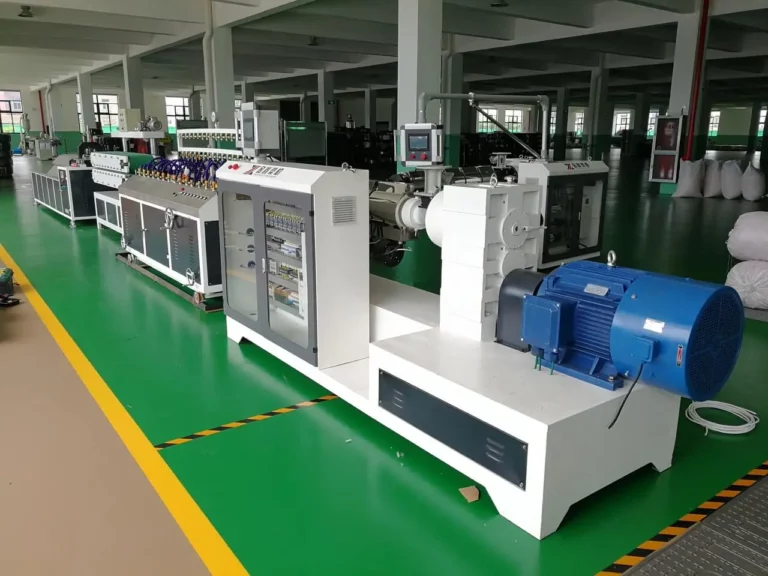
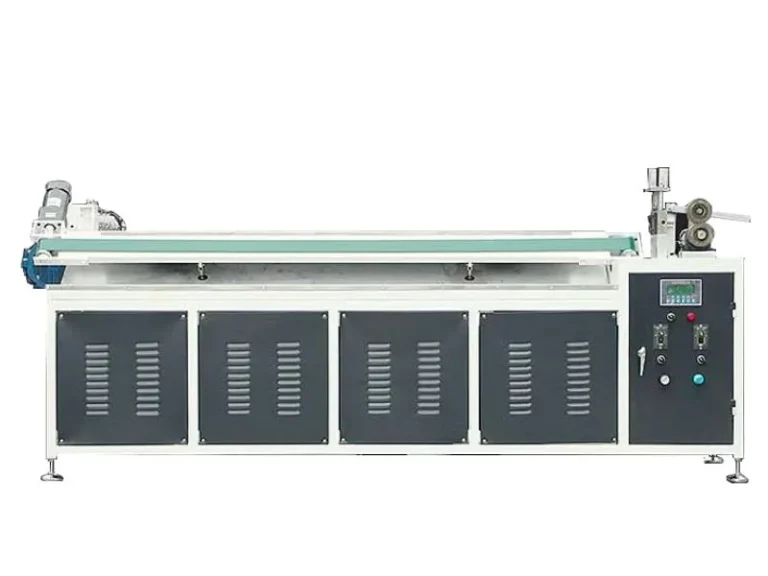
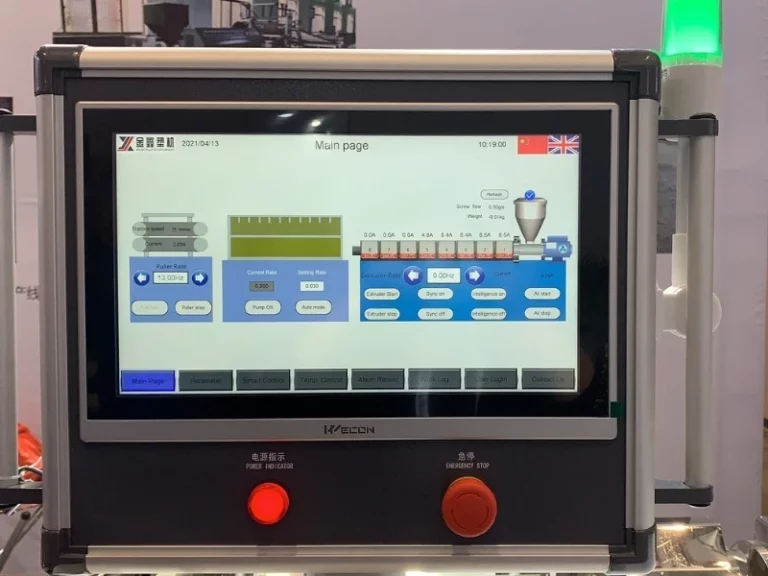
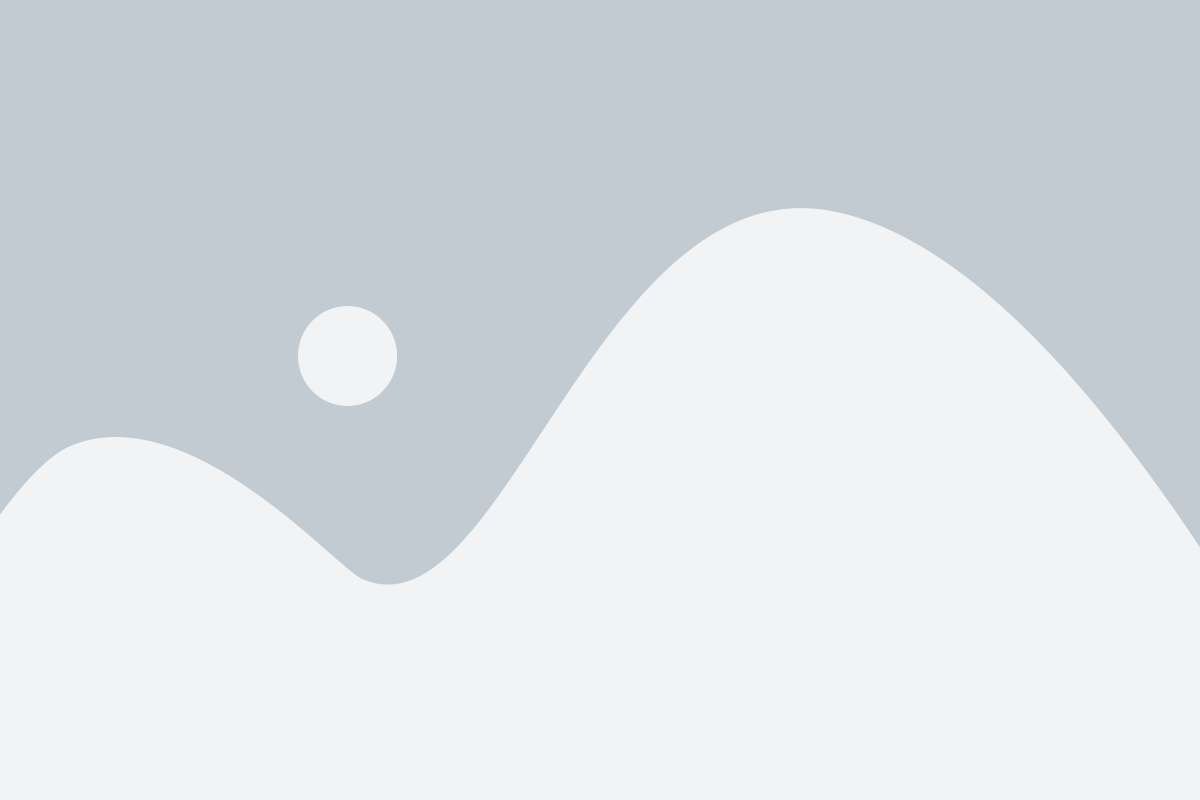
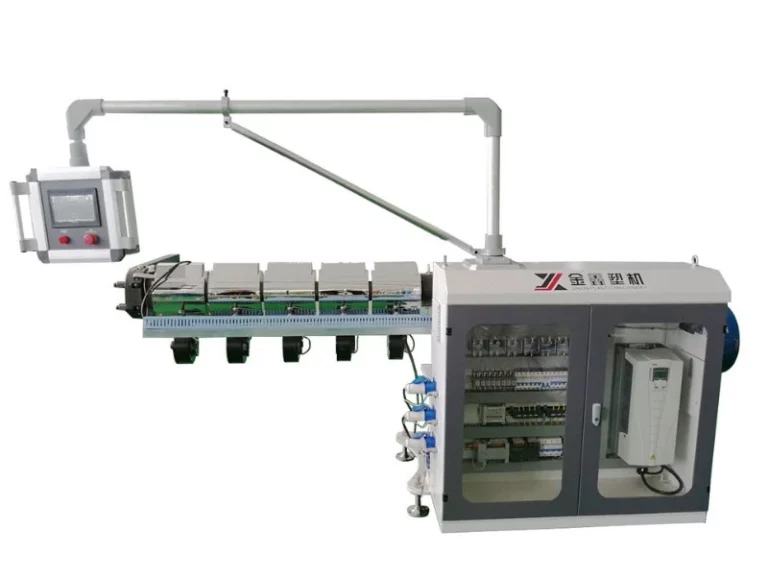
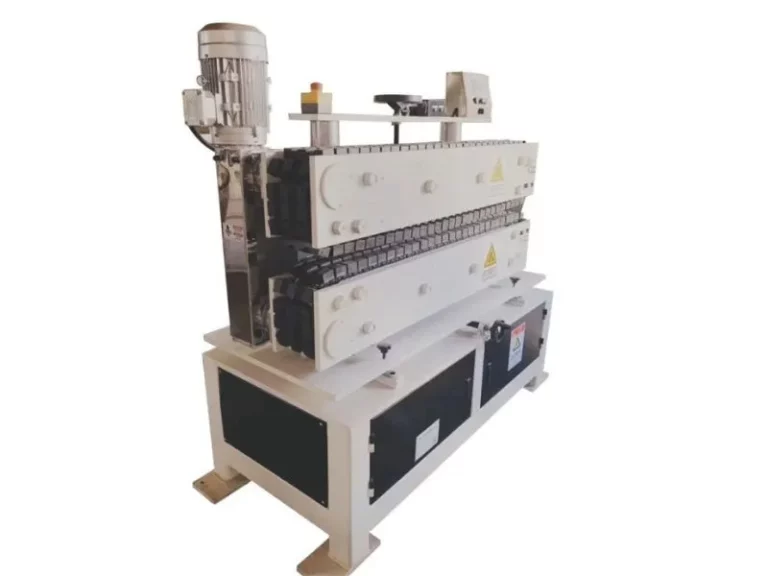
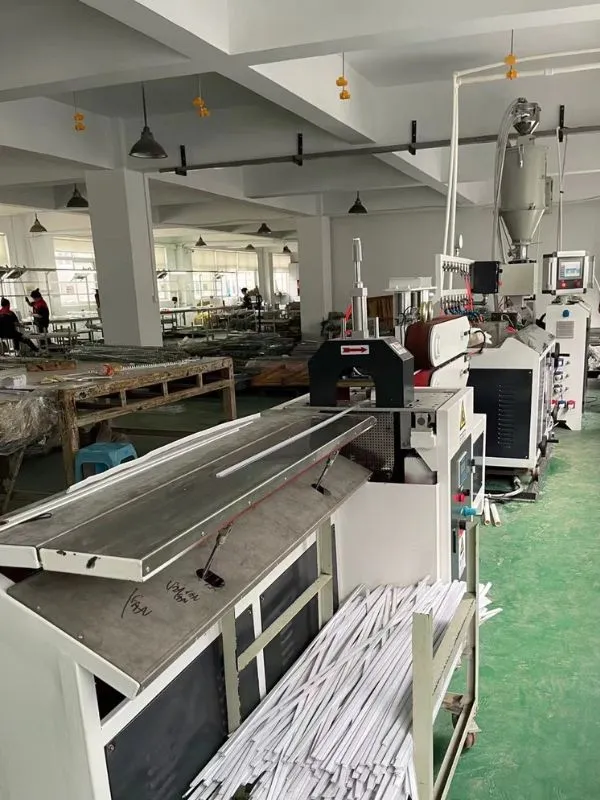
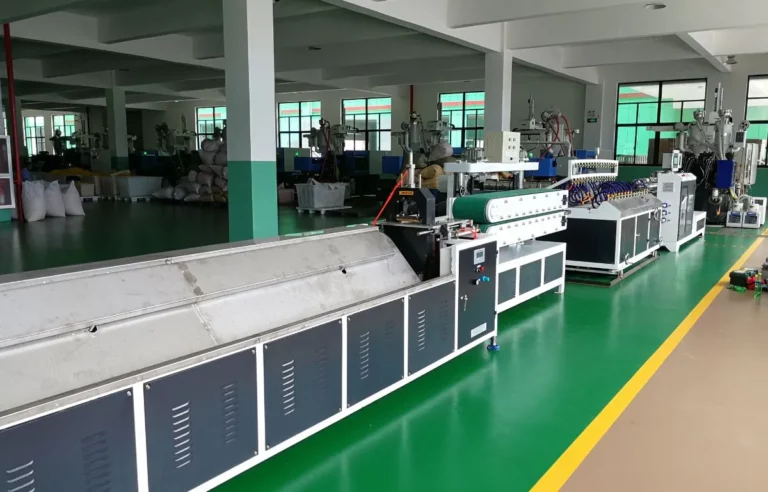
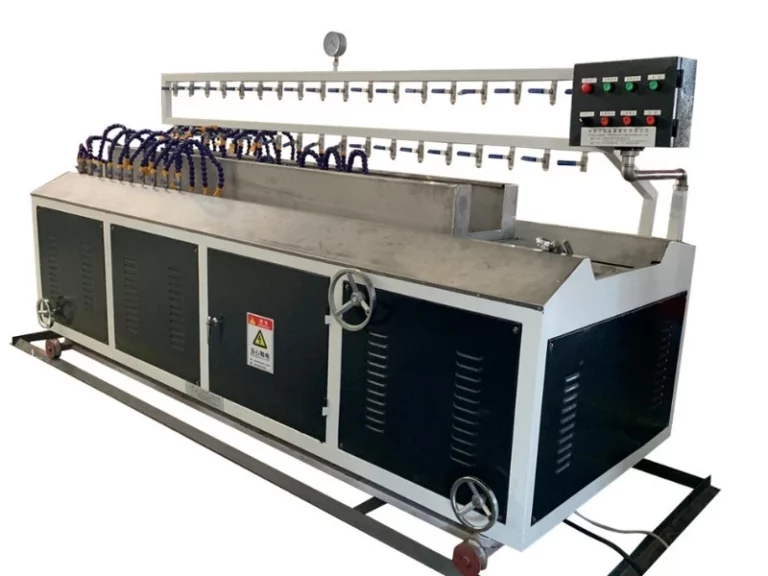
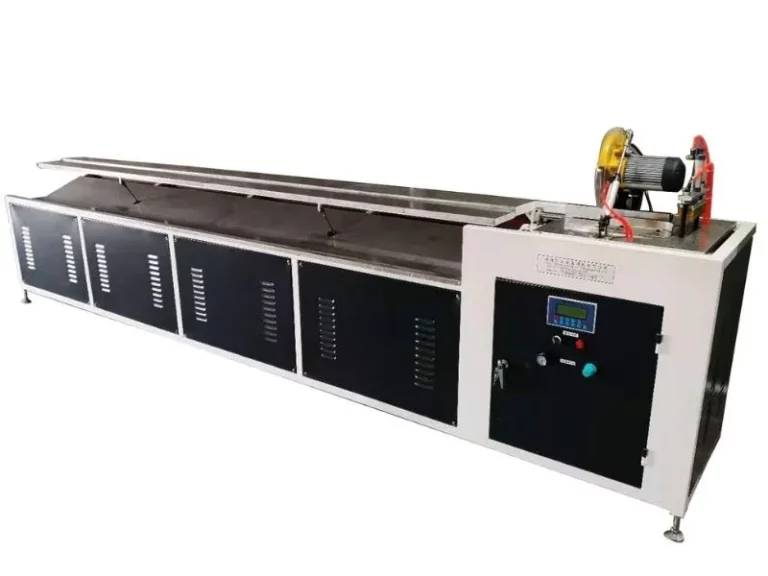
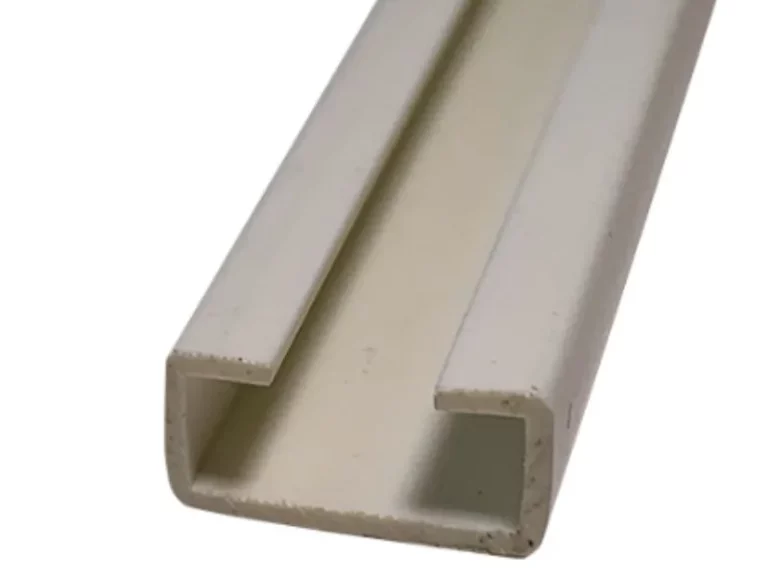
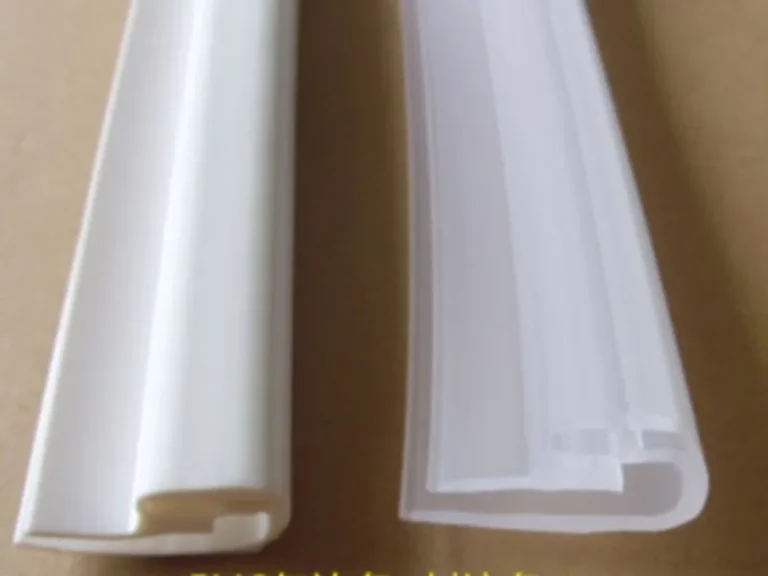
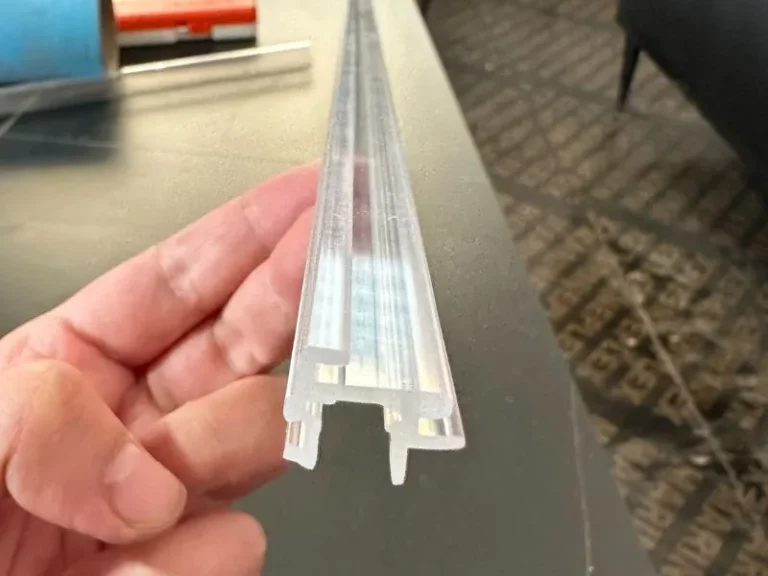
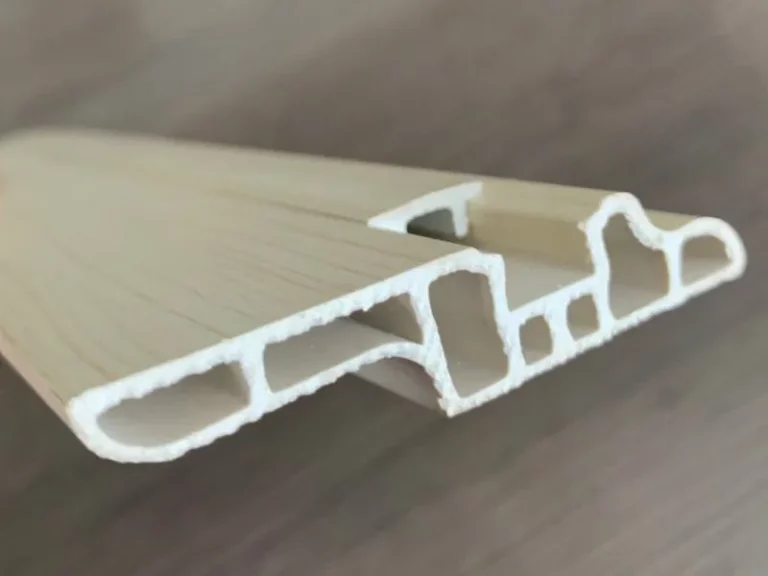
REQUEST A quote
Want to Know More? Discover Our Full Production Line Below
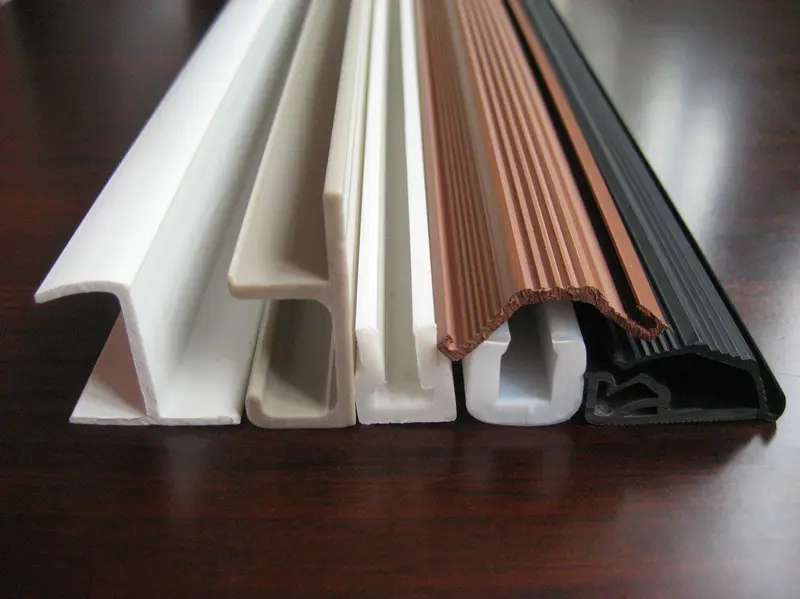
Your Trusted PVC Profile Co-Extrusion Line Solution
Key Components of Our PVC Profile Co-Extrusion Line
General (thermal) extrusion process
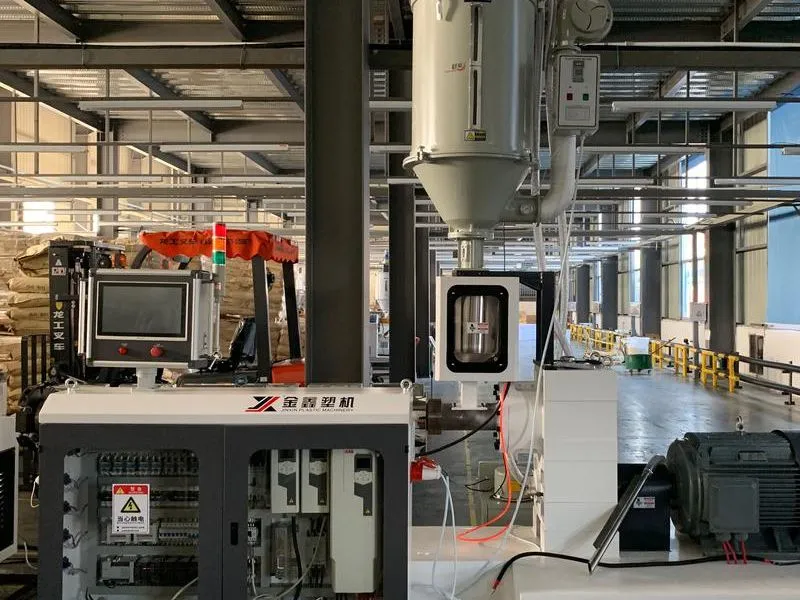
Main Extruder
The single screw extruder is the core of the PVC profile extruder machine line. It melts and mixes the PVC resin with additives to form a uniform melt. This type of extruder is cost-effective and suitable for producing simple profiles and basic applications.
The extrusion die shapes the molten PVC into the desired profile. It determines the profile’s dimensions and surface finish. Precise die design is crucial for producing accurate profiles with minimal defects.
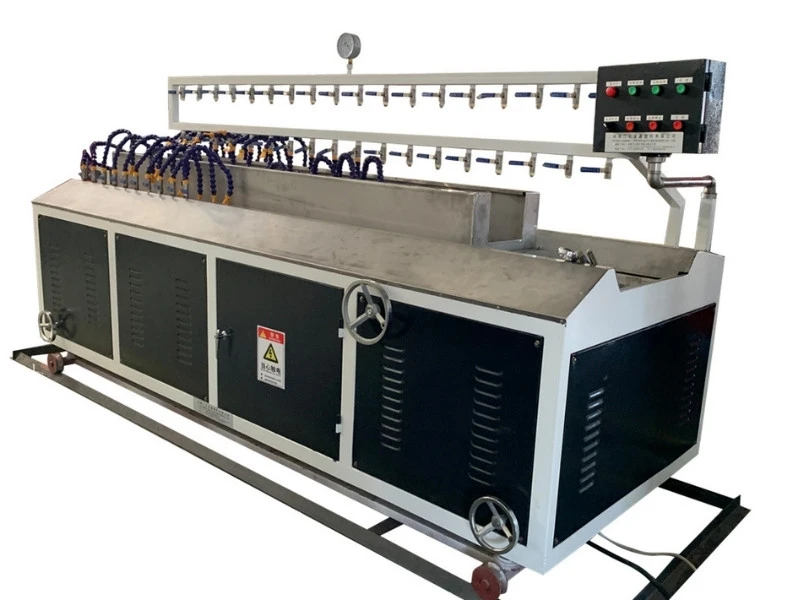
Vacuum Sizing Tank
After shaping, the profile needs to be cooled to retain its shape and dimensions. The cooling system often includes water tanks where the profile is immersed to cool rapidly.
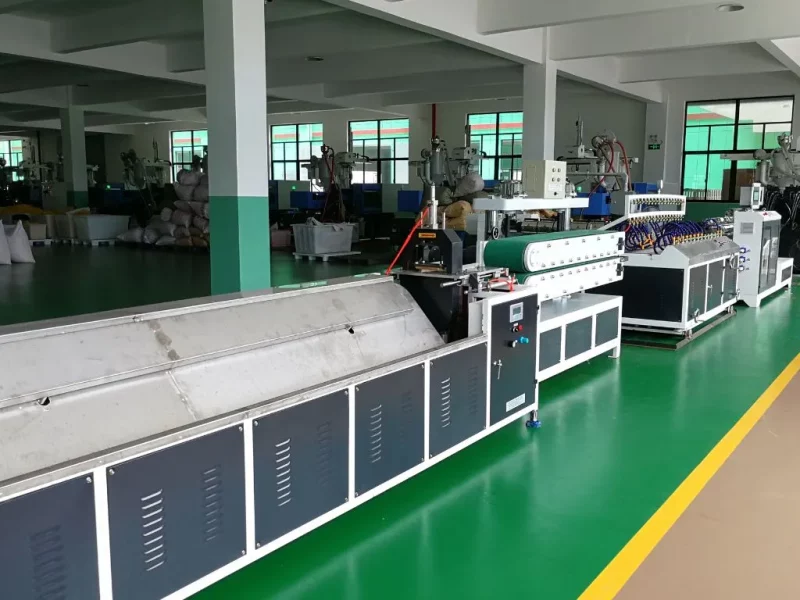
Haul-Off Machine and Cutting Machine
This machine pulls the profile through the extrusion line at a controlled speed, ensuring that the profile maintains its dimensions and consistency. The speed of the haul-off machine must be synchronized with the extrusion speed to prevent stretching or compression of the profile.
Cut the continuous profile into specific lengths and stack them for further handling. Precision cutting ensures clean edges and accurate dimensions, which are vital for the final application of the profiles.
Comparison of Cold Extrusion and Hot Extrusion Processes for PVC Profiles
Hot Extrusion (Vacuum Forming Extrusion)
- Process Characteristics:
- Surface Quality: Typically results in a matte finish with potential surface defects like pull lines and shrink marks.
- Material Use: Suitable for PVC products with filler content below 30%.
- Production Efficiency: High production speed and efficiency, making it ideal for high-strength and tough profiles.
- Dimensional Precision: Profiles may have larger tolerances compared to cold extrusion.
Cold Extrusion (Cold Top/Hard Top Forming)
- Process Characteristics:
- Surface Quality: Achieves a mirror-like, high-gloss surface.
- Material Use: Capable of using high filler content materials, such as high calcium components, which reduce raw material costs.
- Production Efficiency: Lower production speed and efficiency compared to hot extrusion. Suitable for profiles requiring high surface quality.
- Dimensional Precision: Produces profiles with very tight tolerances and high precision.
Advantages & Disadvantages of Hot Extrusion (Vacuum Forming Extrusion)
- Advantages:
- High Efficiency: Fast production speeds, ideal for high-volume manufacturing.
- Good Strength and Toughness: Produces profiles with strong structural integrity.
- Cost-Effective for Low Filler Content: Best suited for profiles with filler content below 30%.
- Disadvantages:
- Higher Mold Costs: More expensive due to the need for complex molds.
- Surface Quality: Matte finish with potential for surface defects, such as pull lines and shrink marks.
- Larger Tolerances: Dimensional precision may not be as high as cold extrusion.
- High Equipment Requirements: Requires high-quality extruder configuration and PVC formulation.
Advantages & Disadvantages of Cold Extrusion (Cold Top/Hard Top Forming)
- Advantages:
- High Surface Quality: Produces profiles with a glossy, mirror-like finish.
- Dimensional Precision: Achieves tight tolerances, making profiles fit precisely with CAD designs.
- Lower Raw Material Costs: Can use high filler content, reducing overall material costs.
- Disadvantages:
- Lower Production Efficiency: Slower production speeds compared to hot extrusion.
- Reduced Strength and Toughness: Profiles may be less tough and strong due to high filler content.
- Handling and Surface Protection: Requires protective measures such as coatings or PE bags to prevent surface damage during handling and transportation.
PVC Profile Co-extrusion Line Related Q&A
May help you know more
How do you ensure proper bonding between soft and hard PVC layers in co-extrusion?
We select PVC materials with matching melt properties for seamless bonding. Our equipment maintains precise temperature and pressure to prevent delamination. Plus, our precision molds ensure consistent layer alignment for a flawless finish.
What is the differences between Hot and Cold extrusion?
- Hot Extrusion: Suitable for general PVC profiles where high production efficiency and strength are prioritized over surface finish.
- Cold Extrusion: Ideal for high-quality applications requiring a superior surface finish and precise dimensional accuracy, such as window frames, stair handrails, cable ducts, and skirting boards.
Can your co-extrusion line handle different hardnesses of PVC in a single profile?
Yes, our line is designed for both soft and hard PVC co-extrusion. It produces multi-layered profiles with varying hardnesses, like flexible seals and rigid frames. Quality remains consistent across all layers, no matter the hardness.
About JINXIN Plastic Machinery
Since 2012
We are honest and reliable, providing cost-effective equipment for your factory
By choosing our equipment, you are partnering with a supplier dedicated to resolving your pain points with expertly curated, high-quality, and cost-effective solutions. We stand by the reliability and performance of every product we offer, ensuring that your investment delivers the results you need for your business to thrive.
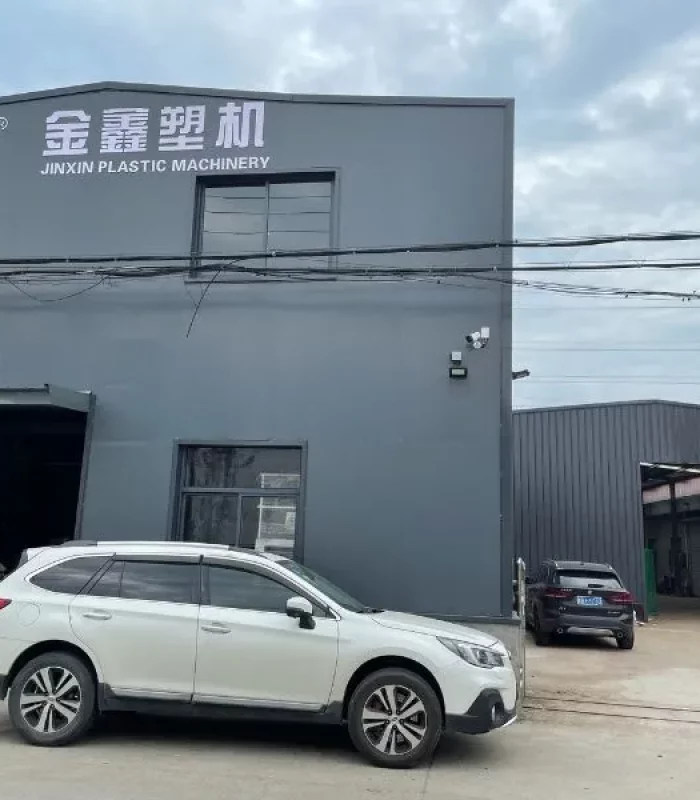
Proven Quality
Over a decade of experience and customer feedback ensures our selected machines offer long-term durability and reliable performance.
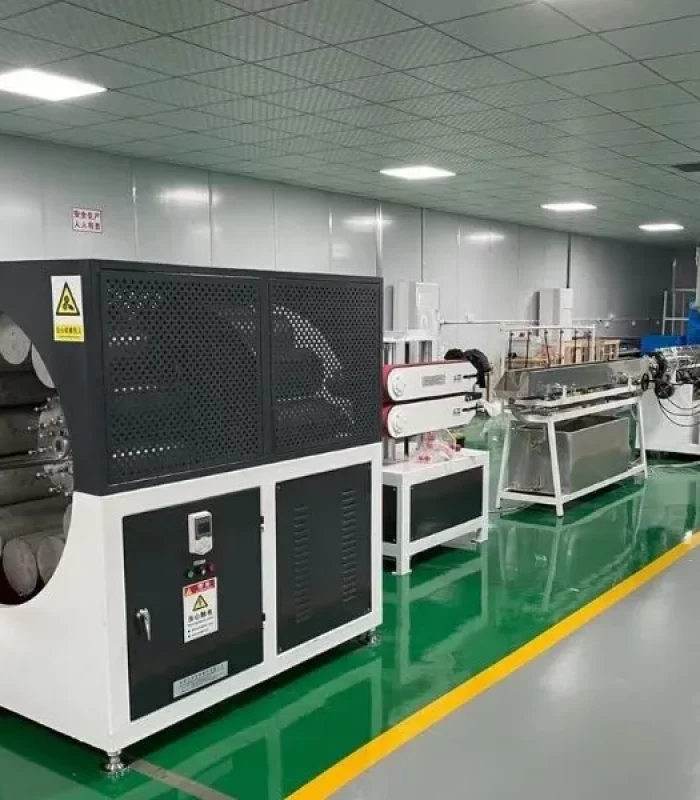
Exceptional Value
We provide high-quality equipment at competitive prices, maximizing your investment with top-tier performance.
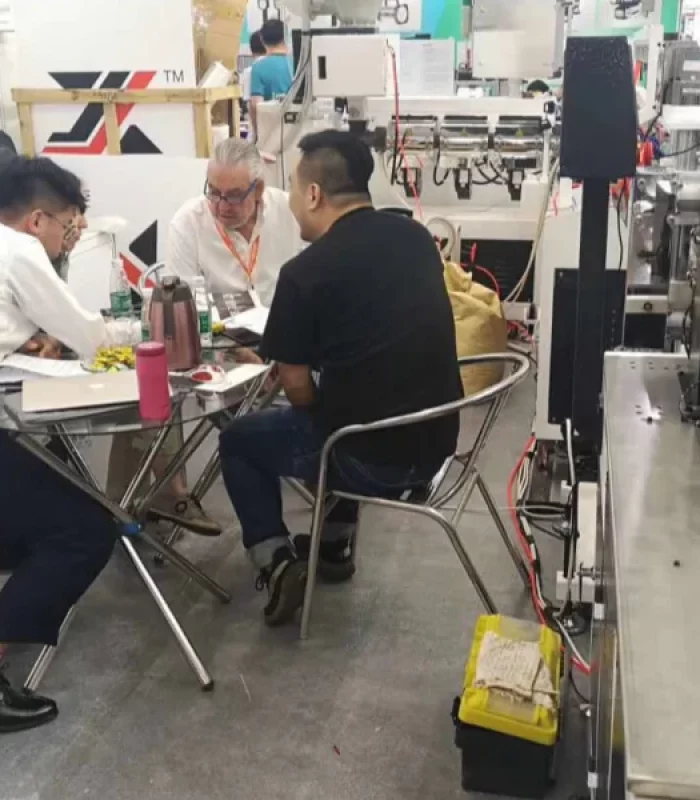
Reliable Support
Comprehensive support and service ensure smooth operation and minimal downtime, maintaining optimal productivity.
Our Customers Say
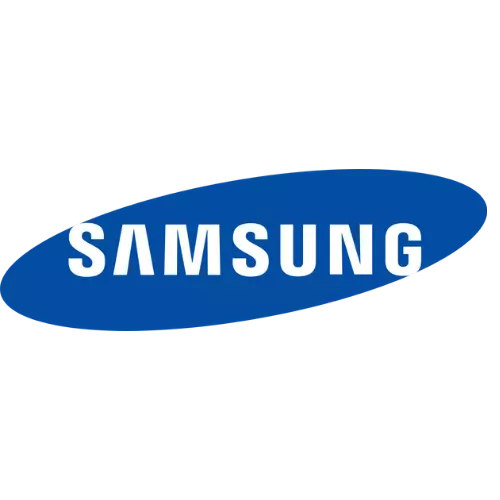
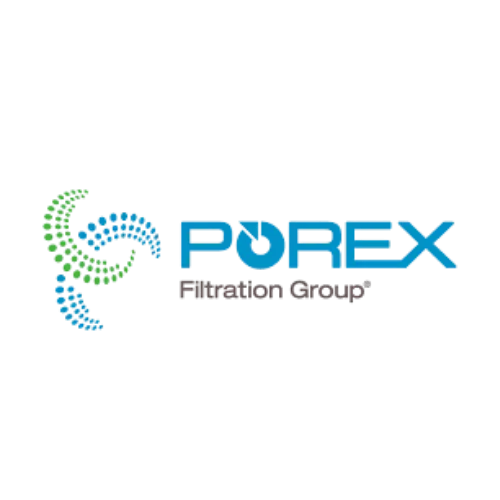
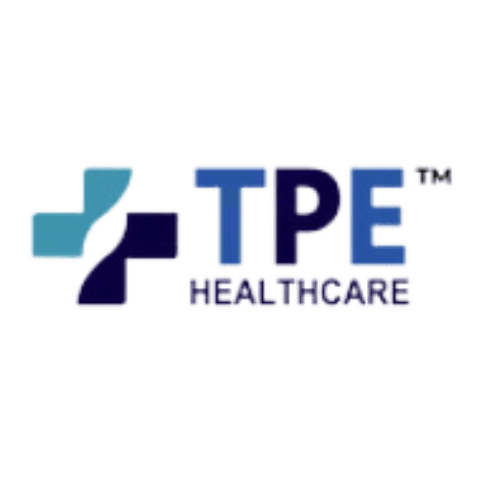
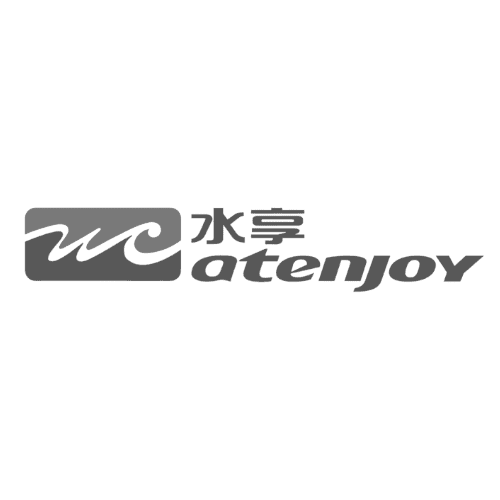
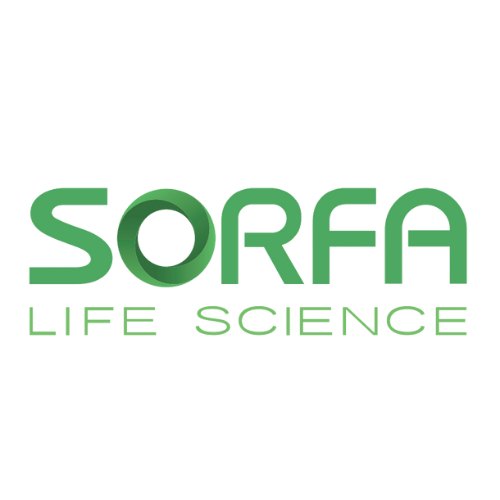
Our amazing Suppliers
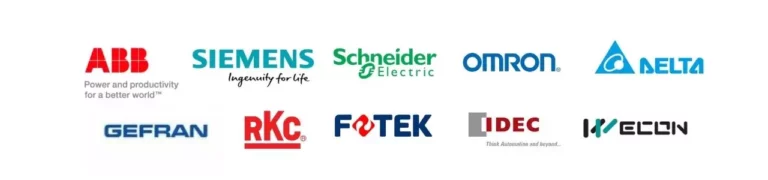
EXTRUSION SOLUTIONS
Email Address
sales@jfextruder.com
Factory Address
No. 31 Yuci Rd., Yuyao, Ningbo City, Zhejiang Province, China