High-Precision Dip Tube Extrusion Machine
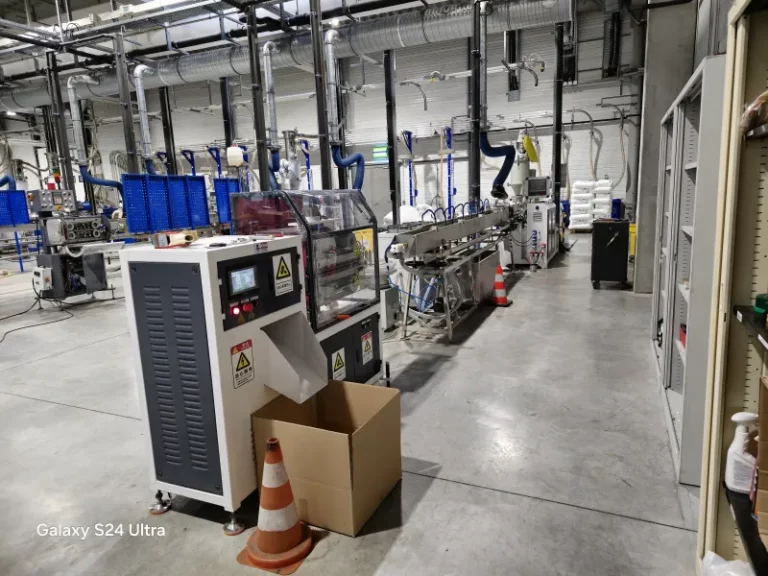
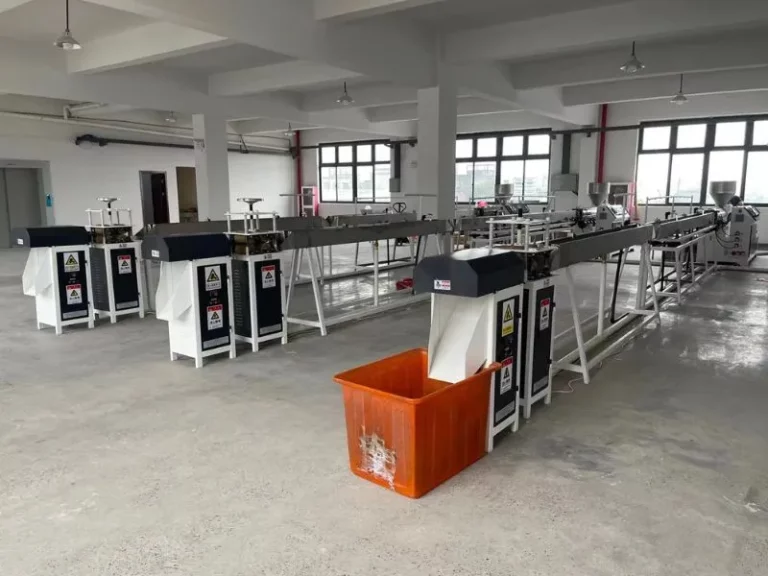
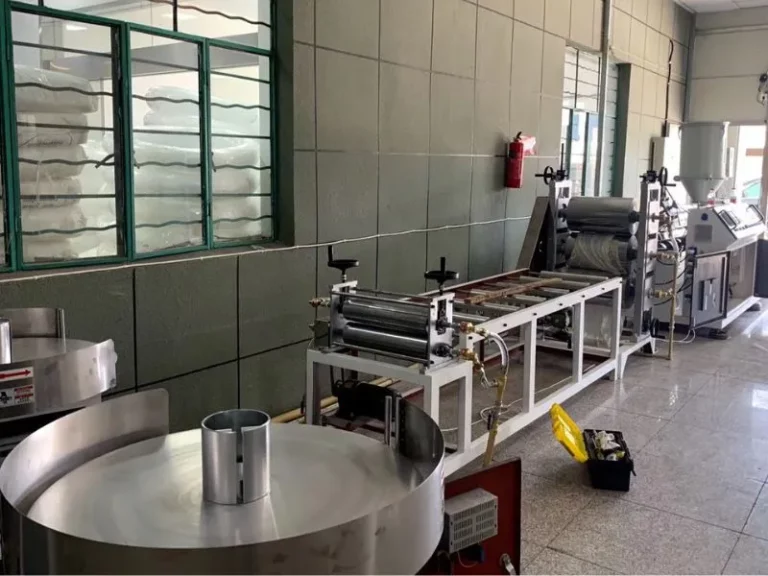
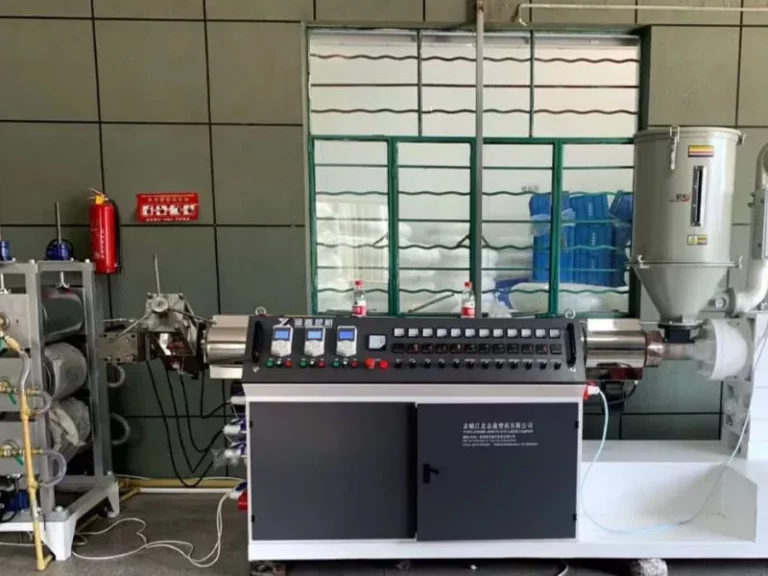
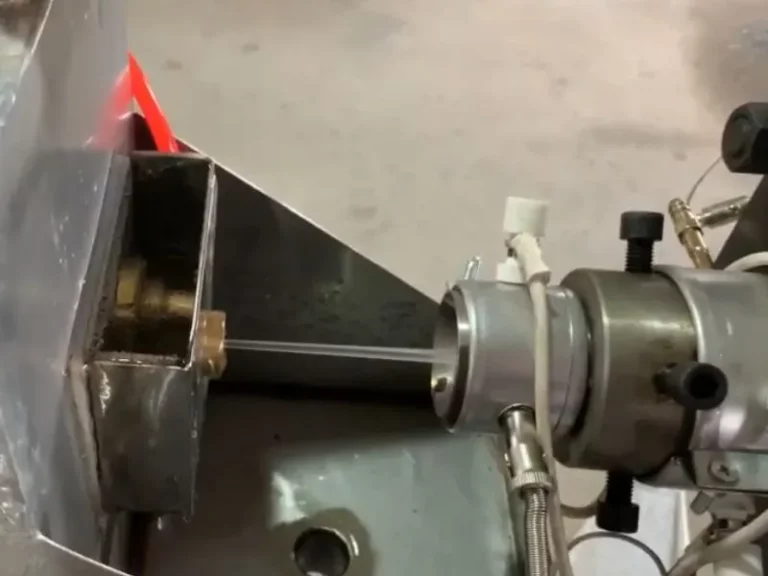
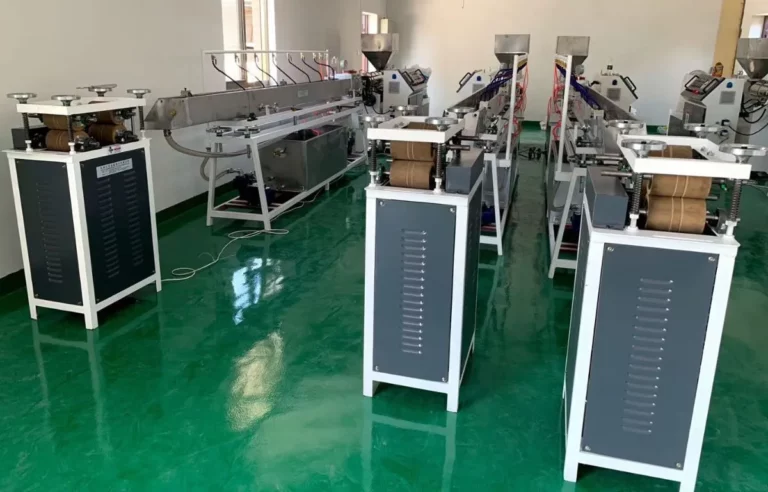
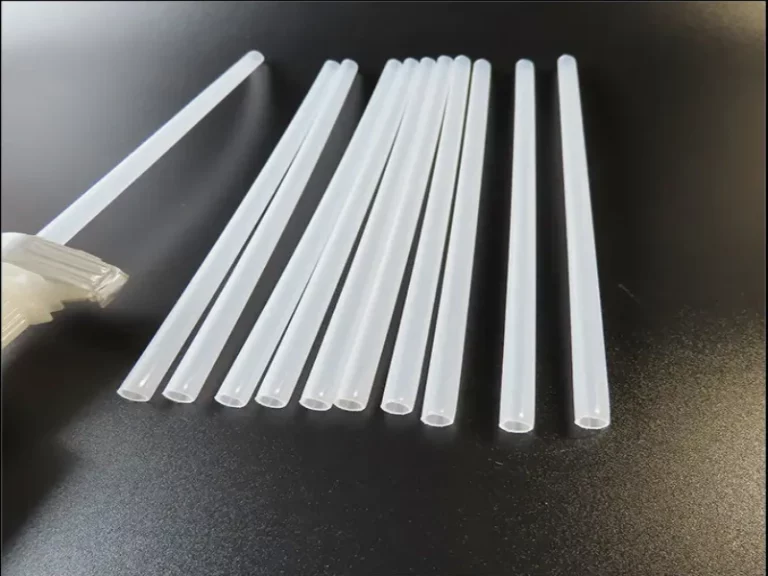
REQUEST A quote
Calculate Your ROI of Dip tube extrusion machine
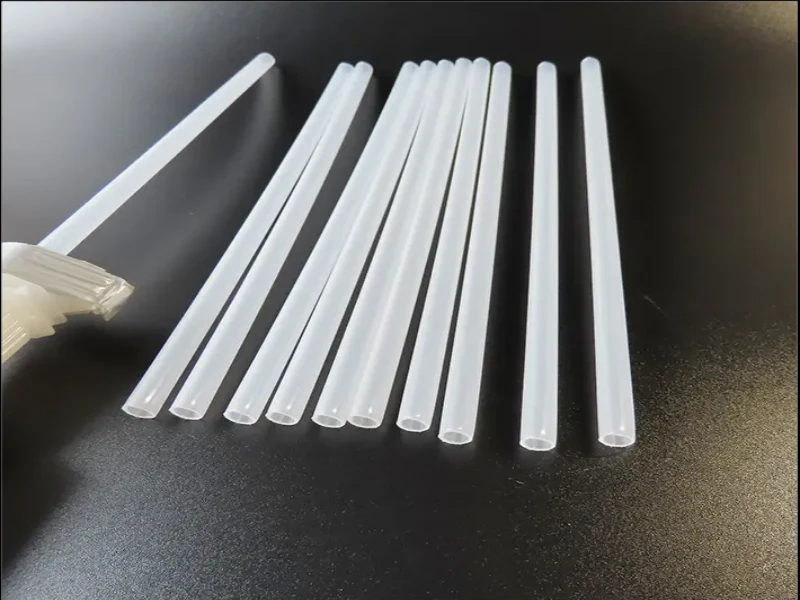
Mastering Dip Tube Production: Inside Our Extrusion Technology
For businesses requiring high-quality dip tubes for packaging, understanding the right manufacturing equipment is key. This section delves into how our Dip Tube Extrusion Machine delivers the precision, consistency, and efficiency you need.
We focus on straightforward benefits: durable machinery that produces exact-spec tubes, minimizing waste and maximizing your output of market-ready products. Explore the components that make our solution a smart investment.
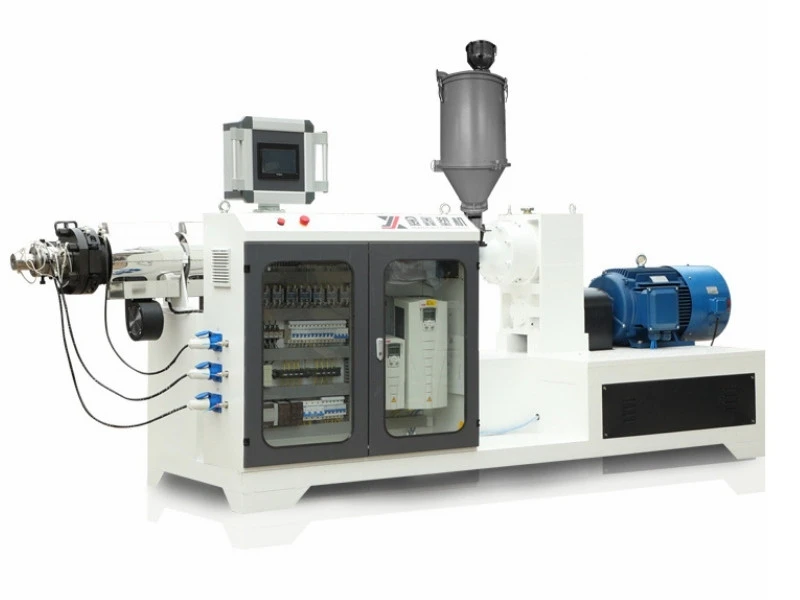
Precision Single Screw Extruder: Consistent Melt Delivery
The core of dip tube extrusion machine line, this extruder is specifically optimized for LDPE and PP.
These polymers are chosen for their excellent properties in producing durable and precise dip tubes.
Our extruder design ensures uniform melting and stable output of these materials, which is critical for thin-walled applications, and promotes excellent plasticization for consistent material flow.
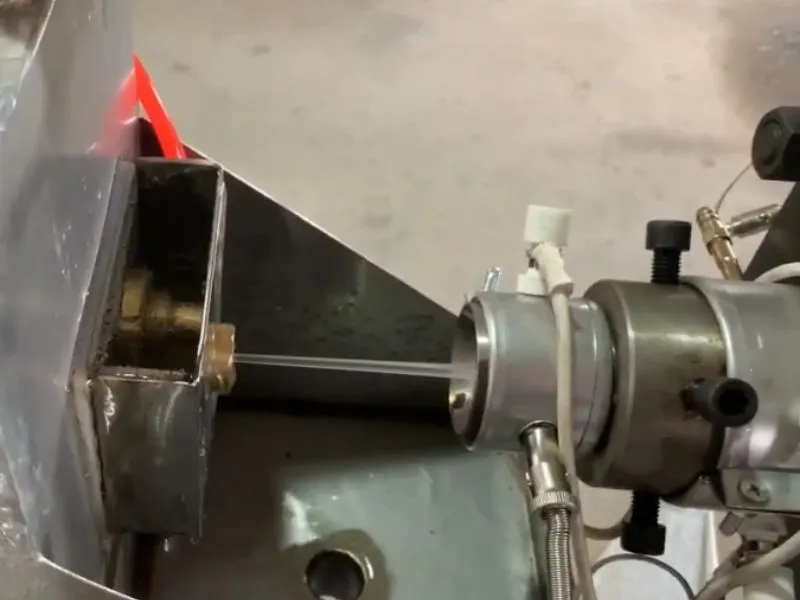
Specialized Die Head & Tooling: Forming Flawless Tubes
Our custom-designed die head and precision tooling are engineered for the small diameters and tight tolerances required for dip tubes.
This ensures accurate tube dimensions, smooth surfaces, and consistent wall thickness, vital for pump and sprayer functionality.
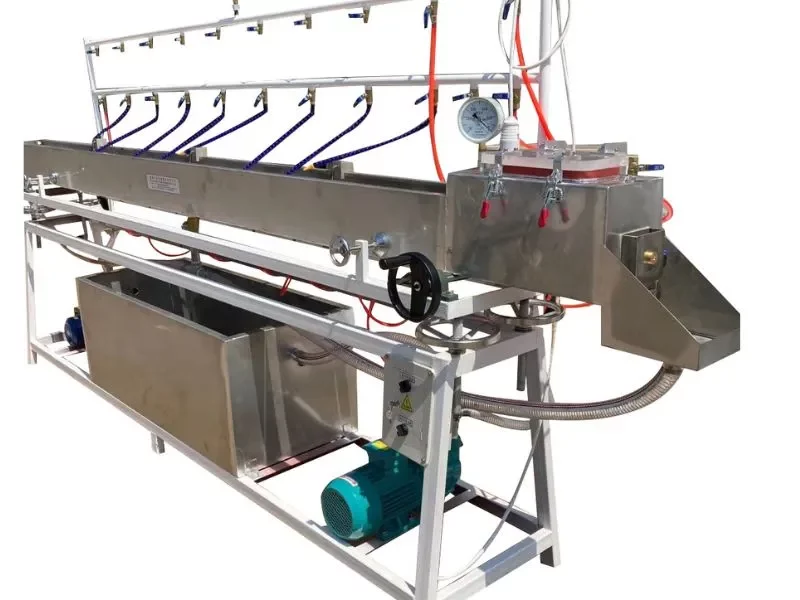
Vacuum Sizing & Cooling Tank: Solidifying Perfection
An efficient vacuum sizing and water cooling system quickly stabilizes the extruded tube, ensuring it maintains its precise circular shape and diameter.
This is crucial for producing high-quality, straight dip tubes ready for assembly.
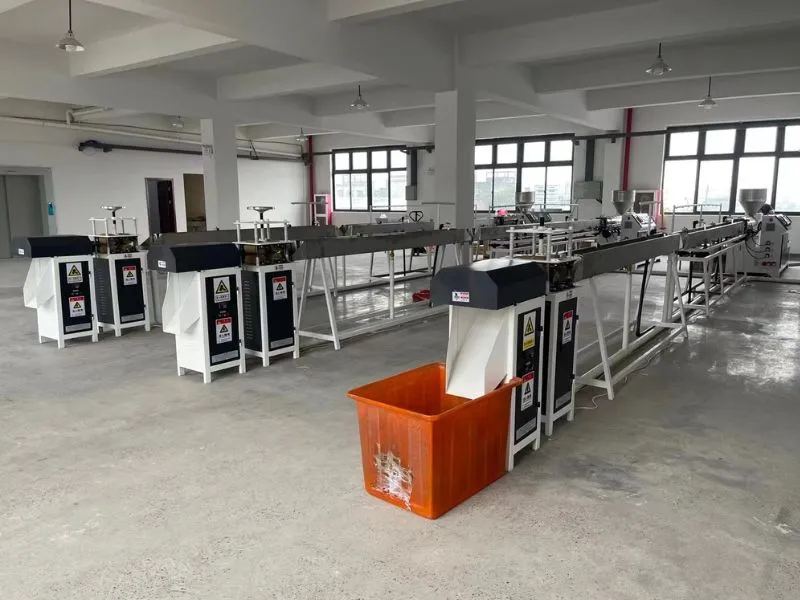
Stable Belt Haul-Off: Gentle & Accurate Traction
The belt-type haul-off unit provides smooth, consistent pulling force, perfectly synchronized with the extruder.
This prevents distortion of the delicate dip tubes and maintains uniform dimensions throughout the production run.
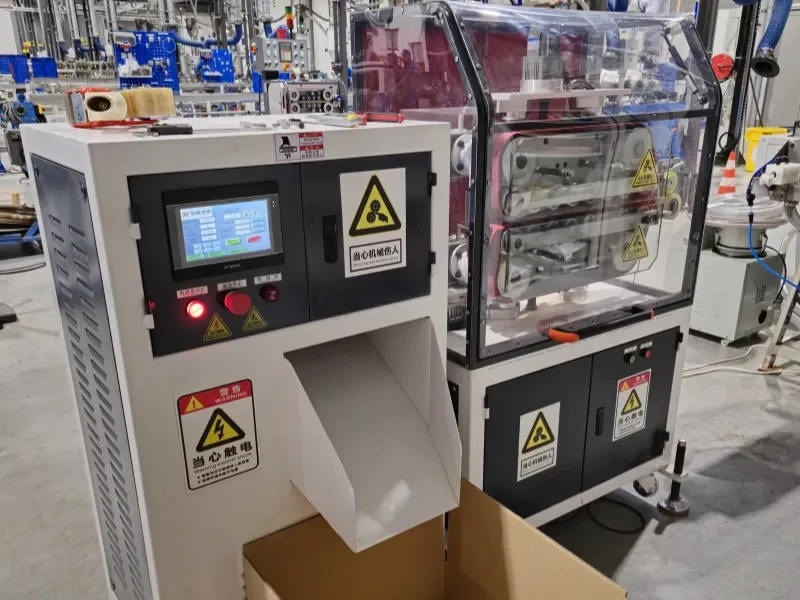
High-Speed Precision Cutter: Clean Cuts, Every Time
Our cutting unit is designed for high-speed, accurate cutting of small diameter tubes, delivering clean, burr-free ends.
This ensures the dip tubes are ready for immediate use in assembly without further processing.
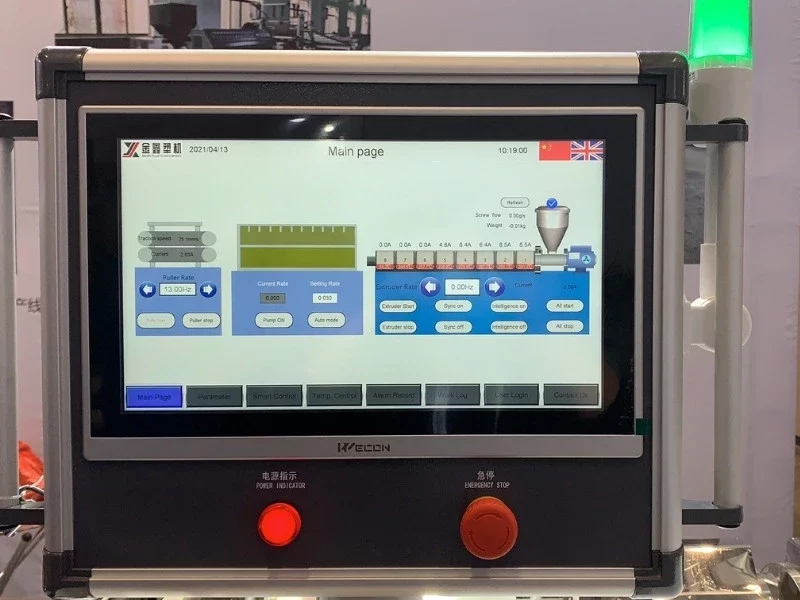
User-Friendly PLC Control System: Effortless Operation
The entire line is managed through an intuitive PLC control system with a touchscreen interface and multi language system.
It allows for easy parameter setting, real-time process monitoring, and quick adjustments, simplifying operation and maximizing uptime.
Precision and Care in Every Detail
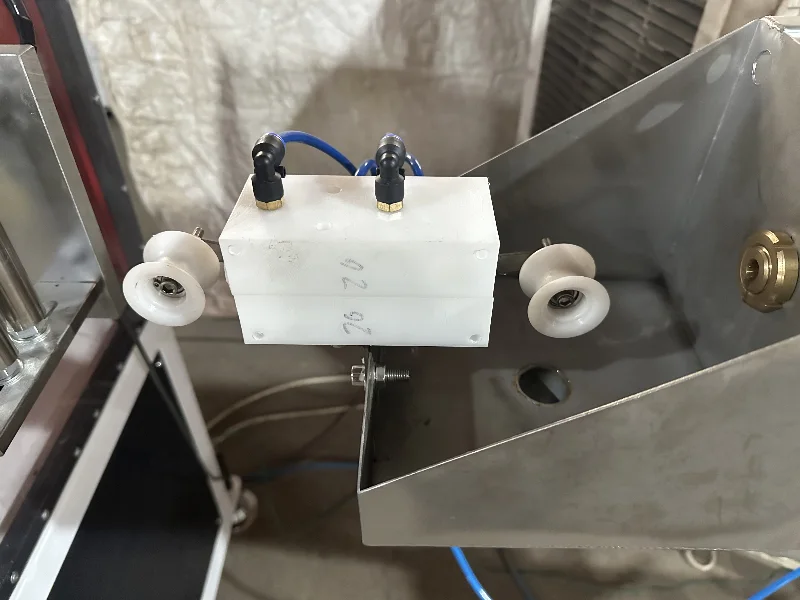
Our dip tube extrusion machine reflects a high level of professionalism and thoughtful design, particularly with the addition of a small air-blowing device at the end of the water tank. Positioned just before the pipes enter the haul-off unit, this feature rapidly dries any residual water, ensuring the pipes are moisture-free.
This serves two key purposes: it enhances the pipe’s final shape for superior quality, and it prevents water from dripping onto the factory floor, reducing the risk of slips and maintaining a safer, cleaner workspace. This small yet impactful detail underscores our commitment to precision and care for our customers’ needs.
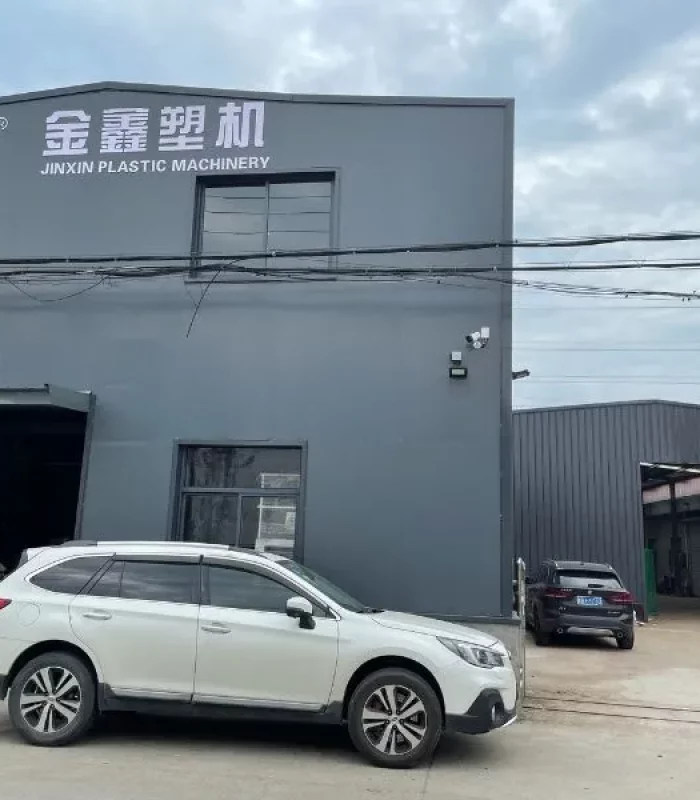
Proven Quality
Over a decade of experience and customer feedback ensures our selected machines offer long-term durability and reliable performance.
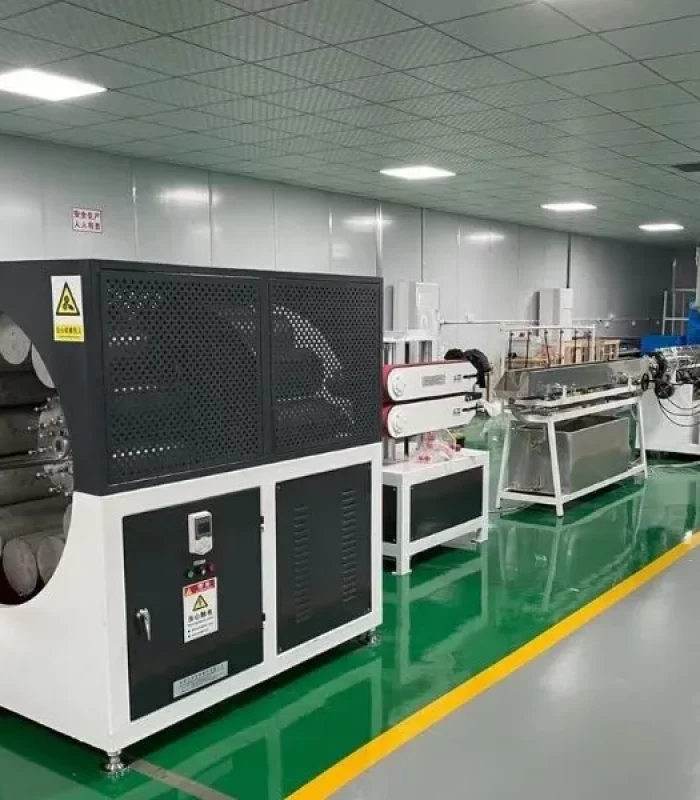
Exceptional Value
We provide high-quality equipment at competitive prices, maximizing your investment with top-tier performance.
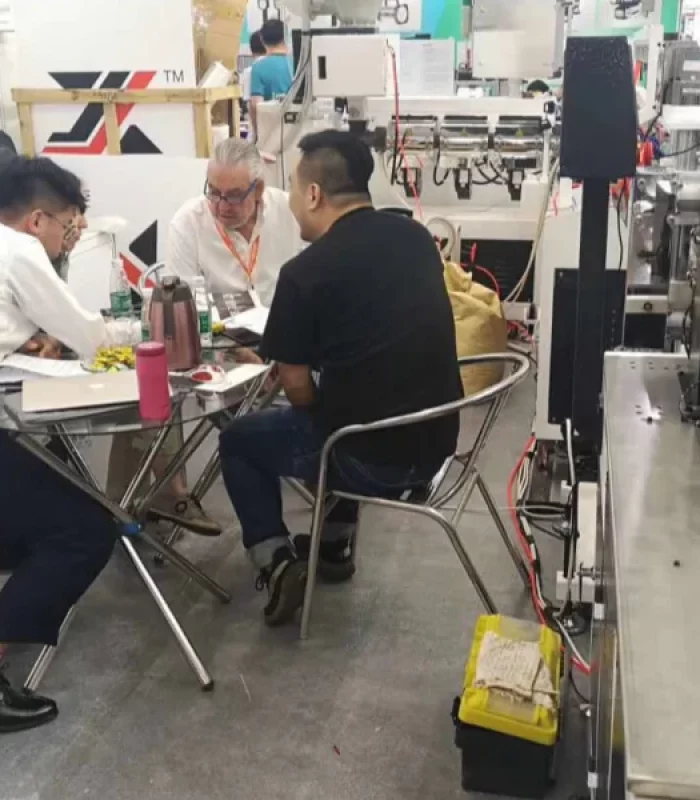
Reliable Support
Comprehensive support and service ensure smooth operation and minimal downtime, maintaining optimal productivity.
Our Customers Say
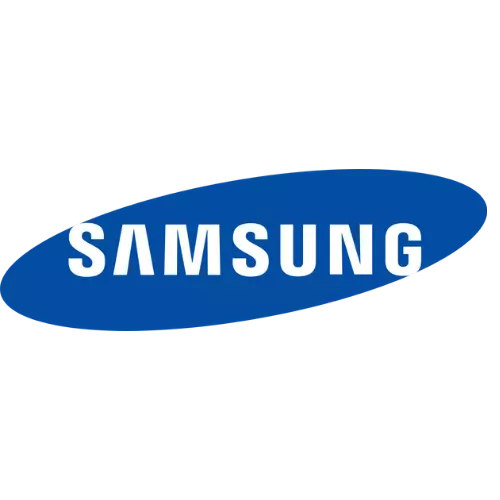
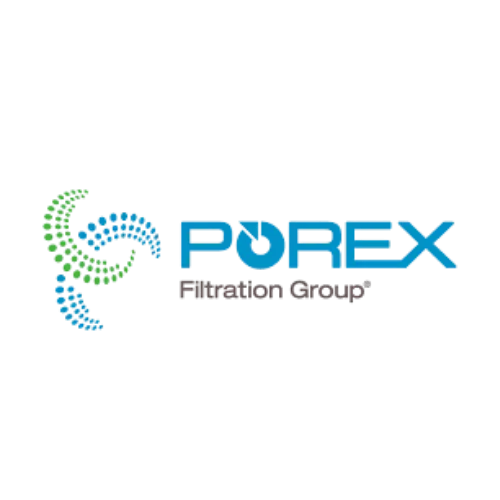
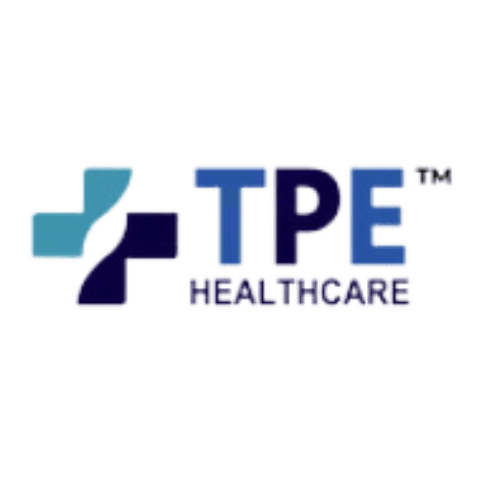
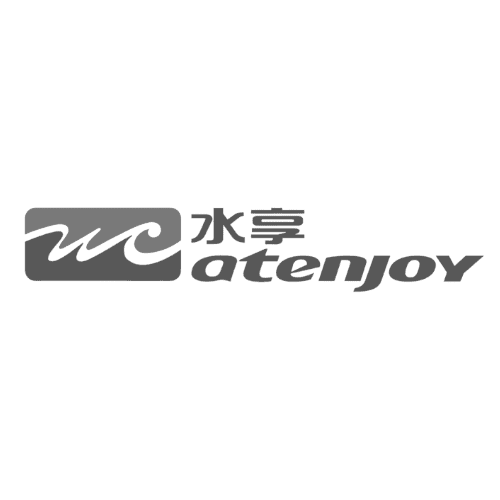
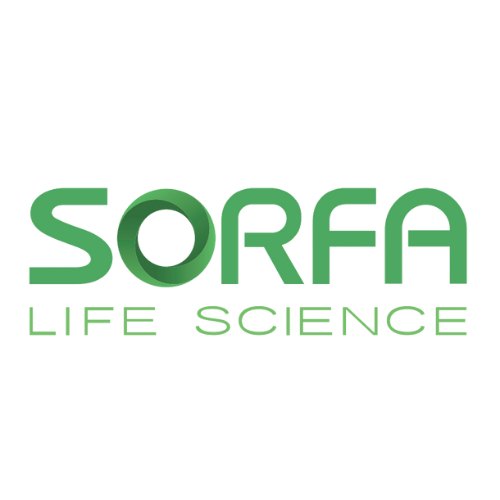
Our amazing Suppliers
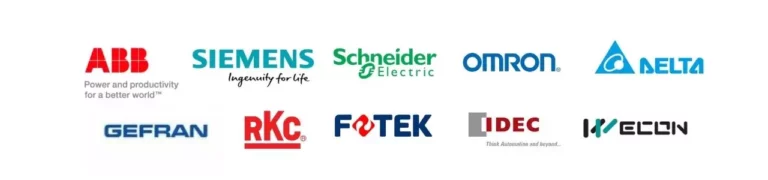
Your Questions Answered: Dip Tube Extrusion Machine
May help you know more
What is the typical range of diameters and tolerances your Dip Tube Extrusion Machine can achieve? This is critical for our pump assembly.
Our machine is specifically designed for small diameter tubes, typically ranging from 1.5mm to 8mm OD (Outer Diameter), with excellent tolerance control, often within +/- 0.1mm, depending on the material and tube size.
We understand precise fitment is crucial, and our system is built to deliver that consistency for seamless integration with your pump and sprayer mechanisms.
We need to produce dip tubes from both LDPE and PP. How easy is it to switch materials on your machine, and does it affect performance?
Switching between LDPE and PP is straightforward. While some purging will be necessary, our screw and die head design facilitates efficient material changeover. We provide clear guidelines for this process.
Performance remains optimal for both materials, as the machine’s heating profiles and screw geometry are designed to handle their specific processing characteristics effectively.
How does your machine ensure the straightness of the dip tubes? Bent tubes cause problems in our assembly lines.
Tube straightness is a key focus. Our system ensures this through a combination of factors: optimized die design for even material flow, precise and stable vacuum sizing that correctly forms and supports the tube during cooling, and a properly aligned haul-off and cutting system.
This minimizes internal stresses that can lead to bending, ensuring you receive straight tubes ready for hassle-free assembly.
EXTRUSION SOLUTIONS
Email Address
sales@jfextruder.com
Factory Address
No. 31 Yuci Rd., Yuyao, Ningbo City, Zhejiang Province, China